|
Category |
Albums |
Files |
| IntroThis first section includes views, a road story and the cool shot of the week, which is a summary of the building process. |
|
5 |
92 |

|
| BasicsThe basics of building the house, including the foundation columns, concrete pour, walls, windows and the roof. |
|
6 |
133 |
|
|
|
Tile
|

|


|
|
The tiling done on this job turned out especially nice. All tiles used on this project are grade A (tiles come in grade A, B and C). The main floor area has a tile with a pink hue and natural pattern (each tile has the identical pattern). Because the pattern is so hard to see, several tiles were inadvertently laid in the wrong way and needed to be chipped out and reset. All areas that needed to be sloped were correctly sloped during the laying of the tiles. This is especially important in the bathrooms, where the level of the floor must slope correctly to allow the water to exit via the floor drain. Also, in the patio this is important so that if water comes in contact with the floor it will flow away from the entry door.
There are many different patterns of tiles used as indicated below.
kitchen: natural stone design 30 centimeter square size for the floor, natural dark green granite 40 * 25 centimeter for the outside of the kitchen cabinets, 20 * 20 brownish hue for the kitchen walls and an eye level row of decorative small design tiles.
patio: natural stone design 30 centimeter square tiles (same as the kitchen floor).
bathrooms: natural stone design 20 centimeter square size for the floors, natural stone tan 20 * 25 centimeters for the bathroom walls, white 20 * 25 pattern for the sink cabinet, and an eye level row of decorative small design tiles.
15 files, last one added on Sep 27, 2011 Album viewed 66 times
|
|
Roof
|

|


|
|
The roof is of course a major part of the house. And now even more so with the popularity of the tile roofs. Heavy tile is a good durable roofing material and not only that: it is very attractive. Its popularity (tile) is due to demand from foreigners building (or buying) houses here. Now, practically every house built for foreign buyers uses the heavy tile. However, it is not the most practical roofing material. First off, it is real heavy. Each tile weighs about 4 kilograms, the roof on this house uses about 3000 tiles, which comes to about 12 metric tons. The weight requires the support structure to use a lot of heavy duty metal. Any problems in the support structure will cause the steel supports to bend. Secondly, the material is brittle. If you walk on it a lot it will chip and crack. Also it is not the most secure material, someone wanting access to your house can get on the roof and remove some tiles to gain entry. That all being said if you ever want to sell your house, it will need to have a tile roof. For more information on roofing materials, please check out the roof info page here!
One thing about this project is that I got to see plenty of development going on and was able to observe many house builders. One thing I can say is that the cool thai house builders did a very exceptional job and really put in a lot of effort to get the job done right. That being said, the roof was really a struggle. This time I went the 'one contract price for all labor to build the house' route (although extra contracts were made to cover electric, some plumbing and other add ons -- which are not a part of the house proper). In further jobs, I will use specialists for specific jobs, especially the roof. I was able to observe a company who specializes in roofs come in and do an neighbors roof and I was very impressed. Back to this house, there were two problem areas with the roof. The first was evaluating how much supporting metal was needed. Observing some metal bending due to stress from the weight of the roof sent me scurrying off to find and engineer (see engineer rip-off). As it turned out the problem was corrected by straightening the metal and adding some supplemental metal supports. The second area was two roof valleys. Under the roof valley there is aluminum gutter drainage. In our case we used inadequate (in size) aluminum drainage which caused countless days of repair work to eventually get it fixed.
One other note about the roof, is be careful when choosing a architect. As my friend Nick noted in the article on the Planning Czar, you can run into problems when getting plans drawn up. As for my experience here, basically the pitch on the roof is steeper than anticipated, but it looks real nice and gives the house and air of superiority. That being said, if I was designing this house again I would lower the roof height (in the middle of the house) from 2.75 meters to maybe 2.25 meters. The additional height caused a lot of extra materials to be used and the added height doesn't add that much.
40 files, last one added on Sep 27, 2011 Album viewed 101 times
|
|
|
|

|
| DetailsThe details of the house, including ceiling layouts, roof eves, the kitchen, bathrooms, and electrical. |
|
5 |
122 |
|
|
Kitchen
|

|


|
|
The approach for the kitchen was to build a nice comfortable kitchen inexpensively. This kitchen measures 3 meters square. Upon entry to the left is an open area in which the wall mount water heater is installed. Then there is the sink area. In the middle portion there is an open area in the counter to allow a stove to be inserted. The counter goes all the way around to the right and on the right hand wall facing the sink the counter ends prior to the wall to allow a space for a refrigerator. There is an exhaust fan and ceiling fan.
Aside from a few minor glitches the kitchen construction progressed smoothly. Towards the end of the project a specialist tiler was hired who did the tiling and plumbing in the kitchen. The materials cost for the kitchen, not including the hot water heater, would be around 17,000 Baht as follows, ceiling fan = 1,000, exhaust fan = 1,000, tile = 4,000, sink = 3,000, cement = 1,000, hot/cold faucet = 2,000, plumbing = 1,000, cabinet doors = 4,000
24 files, last one added on Sep 28, 2011 Album viewed 75 times
|
|
|
Electrical
|

|


|
|
The original guy doing the electric wasn't too knowledgeable about electric. Finally we found a electrician within the neighborhood who turned out to be a great help. For a small project like this there is a lot of electric components.
First off, the house uses grounded electrical throughout. This isn't the standard yet, by in large part due to the fact that most electric appliances don't come with the ground plug. However, now they are starting to require that all new houses install grounded electric. When the electric department inspector came to inspect the electric to give the OK to switch on the permanent city power, the inspector was asking questions about the ground. He wanted to know the size of the ground wire, the size of the metal with is to earth and how deep the metal runs in the ground. In this case; the metal rod runs into the ground 1.8 meters, it is 4 hun, the ground wire (grounding electrode conductor) is size 16. In any event he approved the electrical, and then went to do other houses which I know for sure were done without grounded electrical. These got passed also, but who knows if payola was involved. In the last rental house I was in, if I wanted to plug in a USB cable to the back of my computer I would switch off the computer and then turn off the power. Sometimes I would still get a shock which always puzzled me. In any event, here the computer can be touched at will and there is no shock!
There are 35 recessed lighting receptacles and 5 ceiling fans on the ceiling. Each ceiling fan is controlled by its own control box which has separate off/on and rotate switches. In the main entry area the lighting is controlled by 2 dimmer switches. There is a wall mounted reading light in the entry area that is controlled by its own switch. There are two three way switches, one controls the patio lighting and the other controls the lighting in the back of the house. These switches work in combination with an inside and outside switch, and I can say this is a really nice feature. For example, when you come home at night you can switch on the outside light from the outside, but they can also be switched on or off from the inside. There is lighting on the front and the sides of the house all controlled by separate switches. There is also a security light in the front of the house, controlled at the main switchbox upon entry to the house. The perimeter wall lighting is controlled by a switch at the main switch box.
The two water pumps have an outside switch box, but both feed into one station on the circuit breaker. The circuit breaker has eight stations as follows; kitchen, hot water heater, small bathroom (along with the outside lighting and dining area), office, bedroom, large bathroom, pumps and finally the entry room.
26 files, last one added on Sep 28, 2011 Album viewed 78 times
|
|
|
|

|
| OtherThe details of the perimeter wall, water system and gate. |
|
6 |
73 |
Perimeter Wall
|

|


|
|
Walls that are built from concrete blocks are durable and sturdy. An added bonus is that they also help hold in the fill dirt. Fill dirt is often on of the most critical aspects of a house, for if the house is constructed 'too low' -- there is no repair after the fact. With this house we did a partial fill at the beginning to level the land. Then the wall was partially completed, and more fill dirt was brought in the raise the land level another 20 or so centimeters.
The important steps in the process, which are illustrated below are: 1.) Post holes are dug every 2.5 meters. 2.) Support rebar structures are hand made by cutting, bending and wiring together cut rebar metal strands. 3.) These support structures are set in a concrete footing in the post hole. 4.) A large can is used to form the cement up to ground level after the base structure is dry. 5.) A strip footing is created, formed using form wood, which is about 10 inches tall and connects the support rebar structures. 6.) The cement blocks are cemented in place in rows. 7.) A form is made so that a concrete post can be poured around the cement blocks and rebar structure. 8.) Stucco is applied and other decorative options, such as affixing red brick blocks around the entry posts.
One other important note is that during the stage when the blocks are being laid, at the end of each row as piece of rebar is extended into the metal framework. This adds strength when the post is poured.
20 files, last one added on Sep 28, 2011 Album viewed 66 times
|
|
|
|
|
|
|
|

|

Last additions - Original Coolthaihouse Build |
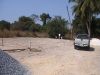
This is the land plot after some fill dirt has been brought in (to the left of the truck). It is 84 square wah. (01-Jan-04) dozerSep 28, 2011
|
|

The resulting paving stone walkway. (12-Aug-04)dozerSep 28, 2011
|
|

The paving stones are set in place.dozerSep 28, 2011
|
|

Fine sand is leveled. (31-Jul-04)dozerSep 28, 2011
|
|

Random files - Original Coolthaihouse Build |

House, left view. (13-Aug-04)dozer
|
|

This is a critical piece of plumbing which is used under the bathtub. Without it, for one thing, foul smells can flow in through the bathtub from the water septic. (24-Jun-04)dozer
|
|

A view of the entry room looking towards the kitchen.dozer
|
|

Attaching a window to the frame.dozer
|
|

Another view of the back wall. dozer
|
|

All of the wood windows have an opening mechanism as pictured here. The window can be opened and closed without having to open the screen. The window is opened by pushing the rod, and closed by pulling it. There is also a locking mechanism on the top of the windows (not shown) which allows the windows to be locked without opening the screen.dozer
|
|

Finishing touches applied to the top of the perimeter wall foundation post.dozer
|
|

Wood framework. (02-May-04)dozer
|
|

|
|
|