|

Top rated - Village House |

Another shot showing the pour of the ground beam. The prefabricated columns have holes which allow the rebar to be affixed to the ground beam. You can see the rebar producing from the column at the 12 o'clock position. The columns are arowan block brand (premium). dozer     (0 votes)
|
|

The form for the ground beam. The ground beam is dug out and formed using concrete blocks. The blocks will be left in the floor. dozer     (0 votes)
|
|

Attaching the grc synthetic corrugated roofing board to the roof structure. Brand of roofing was Elephant, thickness 5 mm. Notice the parallel metal c sections used to form the gutter in the roof valley. dozer     (0 votes)
|
|

The 3" hard wood is hammered into place to create a surface for the fascia board to be attached. dozer     (0 votes)
|
|

More work on the roof. The cross members are set in place. The helper in blue is holding the ground while the foreman welds. dozer     (0 votes)
|
|

The roof apex is 1.5 m above the prefabricated columns. Here the foreman is setting the roof apex in place. dozer     (0 votes)
|
|

Here the foreman is doing the roof structure. The apex of the column is 4 meters (as can be seen imprinted on the top of the column) and is underground about 1 meter leaving about 3 meters. The stick is being used temporarily level the upper room beam. dozer     (0 votes)
|
|

Fill Brought InShows the level of the dirt raised after fill is brought in via a tractor. The tractor was 500 per hour. dozer     (0 votes)
|
|

Fill Dirt after PostsThis build used 4 meter tall prefabricated columns. They were set in footings and allowed to dry for 1 week, then fill dirt was brought in to raise the floor level. dozer     (0 votes)
|
|
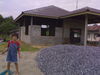
Small worker checks out the progress. dozer     (0 votes)
|
|

Interior wall with electric sunken electric junction box. One row above the box there is a poured ring beam to add strength. dozer     (0 votes)
|
|
|
|

|
|
|